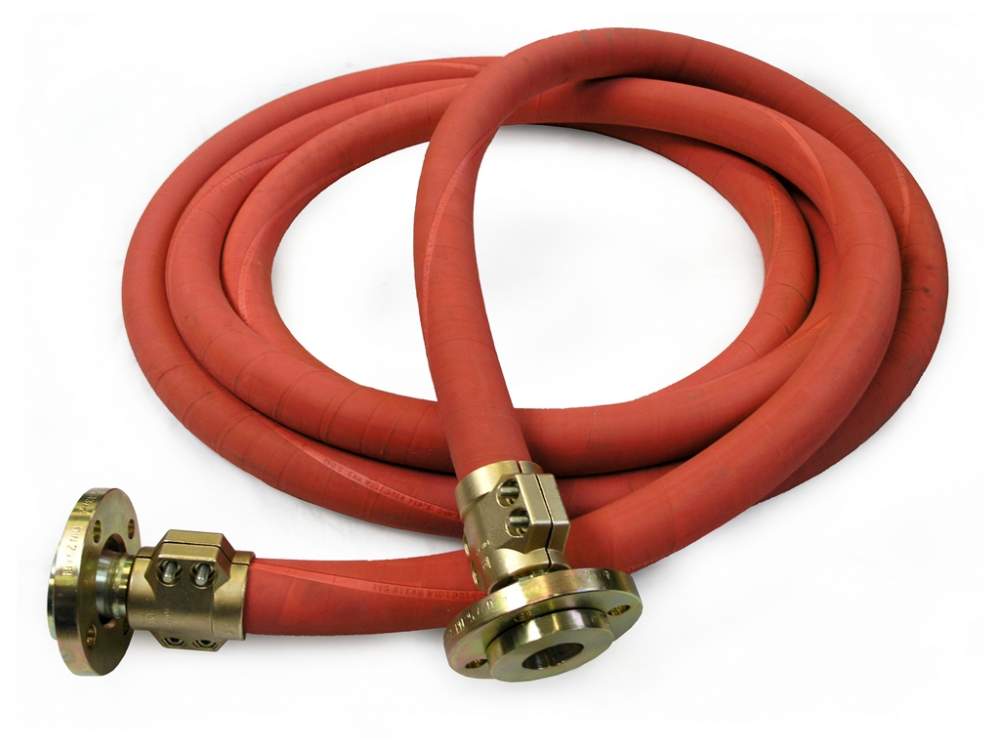
With autumn temperatures returning we are reminded that Old Man Winter is not far behind. Lower temperatures generally mean one thing in the industrial hose world and that is…it must be steam hose season.
With pressures at a minimum of 250psi and temperatures reaching 450 degrees Fahrenheit, we can see the importance of proper hose selection and fabrication. Any company that utilizes steam hose in their day to day operation should know steam hose comes with its risks and rewards. The reward comes with the economic benefits of choosing a proper steam hose for an application and extending the life cycle of the hose, reducing replacement costs and unplanned down time. The burden of course is the risk of a premature hose failure and the potential for damage to property and serious injury to employees. The importance of safety when handling steam hose cannot be stressed enough.
A number of factors are involved with the use and maintenance of steam hose. Following are 5 Steam Hose Maintenance Tips to remember this winter season.
Regular Visual Inspection Intervals
All steam hoses should go thru a routine visual inspection prior to use. This inspection should include checking for wear or damage on the outside cover of the hose. The hose’s end fittings should also be inspected for proper installation. Keep an eye out for excessive rust and wear and tear. If the hose or hose fittings look damaged, do your due diligence to ensure the damage is superficial only, otherwise get a replacement.
Compatibility
The steam hose should be compatible with the application it’s connected to regarding pressure and temperature. Check your manufacturer’s guide to verify the maximum temperature and pressure ratings of your hose. Be sure your steam application will never exceed those maximum limits
Installation
How the steam hose is installed to the application is equally important. The distance between two connection points will ensure equal weight and pressure distribution. This practice prevents the hose from kinking thereby allowing for full flow during use as well as extending the life of the hose.
Handling & Storage Requirements
Proper steam hose handling and storage will combat the rigors of use including extending hose life. Factors to consider relate to the environment the hoses are kept in. Exposure to sunlight, chemical vapors and extreme temperature fluctuation can attack a steam hose even when not in use.
Draining Excess Moisture
Another practice to help increase the life of your steam hose is to thoroughly drain your steam hose after use. Be sure to completely remove all moisture before it is stored and maintained at ambient temperatures to avoid a type of tube deterioration know as “popcorning.” Popcorning is damage that occurs to the inner tube of a hose, ultimately caused by absorption of water vapor into hose tube wall. Once absorbed, the trapped water cools while the hose is not in use. Upon future use, that trapped water rapidly expands when it comes into contact with the high temperature steam causing damage to the tube as it tries to escape. The result is a damaged inner tube that resembles popcorn. Over time, continual popcorning will lead to a hose failure when the damage reaches a critical limit.
Final Takeaways
As you can see there are a lot of considerations when it comes to choosing and implementing a steam hose assembly. To mitigate the risks to employees and equipment and the potential financial loss to your business, it’s best to trust industry experts who can teach and advise you during your hose implementation or replacement process. Summers Rubber Company has been dealing with steam hose applications since the company first opened its doors in 1949. Our inside and outside sales teams can talk you through any scenario or questions you might have. From partnering with premier suppliers such as Continental Contitech USA for our steam hose and Campbell Fittings for our crimp steam hose fittings, Summers Rubber Company is ready to safely guide your business through another steam hose season.
Credit for Content: Gary Garza